Our comprehensive expertise in subsea umbilicals, subsea power cables, IWOCS, and umbilical termination hardware empowers us to deliver complete turnkey solutions tailored to individual operator requirements. The JDR Service division offers installation support and around-the-clock aftermarket support through a worldwide network of highly skilled and fully certified technicians. Our offshore technicians specialise in installation, hook-up, and commissioning, equipped for swift mobilization to any location globally.
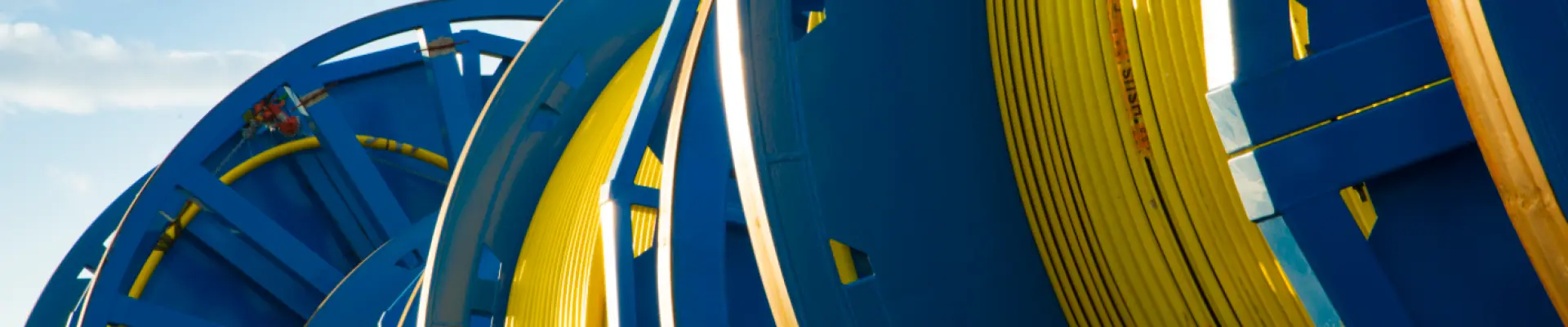
- Main Page
- Markets and Solutions
- Oil & Gas
Markets and Solutions
Energy (Oil&Gas)
JDR engineers and manufactures subsea control umbilicals and subsea power cables for the offshore oil and gas industry. Our products and offshore services constitute an essential component of the subsea infrastructure, facilitating the efficient, safe, and environmentally responsible delivery of energy to end-users.
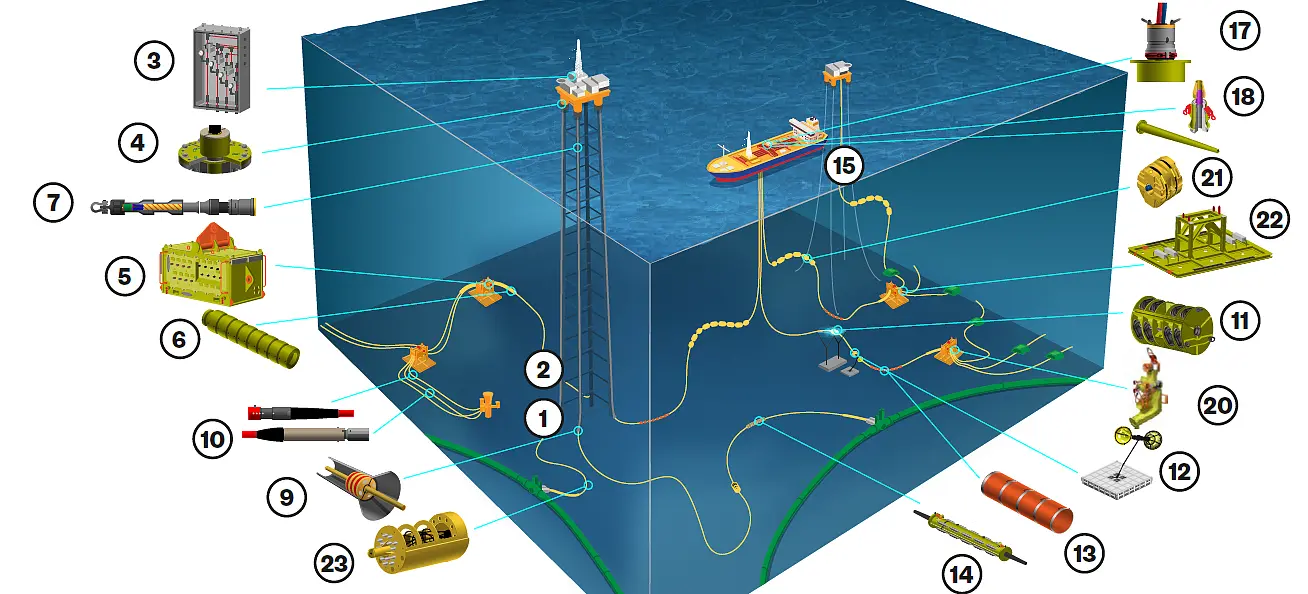
![numery18.png [1.45 KB]](https://www.jdrcables.com/storage/image/core_files/2025/3/11/6fadf014ebf17a8b17bf7d0df4de6838/png/tfkable/preview/numery.png)
A cable design typically used for cables resting or buried on the seabed.
![numery2.png [1.10 KB]](https://www.jdrcables.com/storage/image/core_files/2025/3/11/011970cd43f61fbae188261dfc39b73c/png/tfkable/preview/numery2.png)
An umbilical designed to link surface and seafloor oil and gas equipment for controls, power, or heat. They provide electric and fiber-optic signals, electrical power, and hydraulic and chemical injection fluids to the subsea unit.
![numery3.png [1.09 KB]](https://www.jdrcables.com/storage/image/core_files/2025/3/11/9deab885e540c21f1d6a322aadd88a27/png/tfkable/preview/numery3.png)
Topside connection interface cabinets.
![numery4.png [965.00 B]](https://www.jdrcables.com/storage/image/core_files/2025/3/11/7c598b2494f3d08c98c70429db93ac67/png/tfkable/preview/numery4.png)
The mechanical connection point for
a terminated umbilical onto the host platform or vessel.
![numery5.png [1.14 KB]](https://www.jdrcables.com/storage/image/core_files/2025/3/11/6f7fd3ed11c83af918c991d63a7b4aed/png/tfkable/preview/numery5.png)
UTA connectts the umbilical to the
Subsea Distribution Unit (SDU) which
distributes to multiple users such as trees, manifolds, pumping and boosting stations and infield tie ins.
![numery6.png [1.39 KB]](https://www.jdrcables.com/storage/image/core_files/2025/3/11/88751389d3858fda63005f22025a5884/png/tfkable/preview/numery6.png)
A cable protection device of interlocking
sections which, when subjected to certain bend radius, will lock and prevent further bending of the cable or umbilical inside it.
![numery7.png [1.27 KB]](https://www.jdrcables.com/storage/image/core_files/2025/3/11/a186e65882e6acc70cfce95025fd80a4/png/tfkable/preview/numery7.png)
Used during installation to handle, lift and position an umbilical through
a J-tube to the topside platform.
![numery8.png [1.34 KB]](https://www.jdrcables.com/storage/image/core_files/2025/3/11/318b0f63693e3022f51f7f83b2a7c2e3/png/tfkable/preview/numery8.png)
Connects an SUT with other subsea
equipment to provide electrical signal and power distribution.
![numery9.png [1.39 KB]](https://www.jdrcables.com/storage/image/core_files/2025/3/11/9ba2c8b7c9efe198fd1aa8c6931fa15c/png/tfkable/preview/numery9.png)
A seal to prevent loss of corrosion inhibitor from within the J-tube at the umbilical exit point.
![numery10.png [1.32 KB]](https://www.jdrcables.com/storage/image/core_files/2025/3/11/20ec56710d6fc1d6dcd749a35c1bce53/png/tfkable/preview/numery10.png)
Connects an SUT with other subsea equipment to provide hydraulic control and chemical injection distribution.
![numery11.png [1.14 KB]](https://www.jdrcables.com/storage/image/core_files/2025/3/11/6a9beefcb790f73650eee115bff5e54d/png/tfkable/preview/numery11.png)
A clamp to locate the umbilical between
upper and lower catenaries of the
dynamic system.
![numery12.png [1.41 KB]](https://www.jdrcables.com/storage/image/core_files/2025/3/11/befd0526f0026e0e3fa1d4b0413f80f5/png/tfkable/preview/numery12.png)
A clamp on the seabed to hold an umbilical or cable in position and prevent excessive movement at the touch-down point.
![numery13.png [1.44 KB]](https://www.jdrcables.com/storage/image/core_files/2025/3/11/75c95bf5c7acd17c85d1b8279997680f/png/tfkable/preview/numery13.png)
Prevents abrasion of a cable at a point of dynamic movement.
![numery14.png [1.33 KB]](https://www.jdrcables.com/storage/image/core_files/2025/3/11/873616c7305192b3c25b2142333e02fb/png/tfkable/preview/numery14.png)
Connects two umbilicals or repairs a
damaged umbilical.
![numery15.png [1.47 KB]](https://www.jdrcables.com/storage/image/core_files/2025/3/11/cd0bb6363a67333a2ed8c40d3808a4da/png/tfkable/preview/numery15.png)
Designed to operate within dynamic
subsea environments.
![numery16.png [1.46 KB]](https://www.jdrcables.com/storage/image/core_files/2025/3/11/887910f09e93ff7b56c5e4bcde09c26b/png/tfkable/preview/numery16.png)
Designed to operate within dynamic
environments considering project specific environmental conditions, stiffness and ballast requirements.
![numery17.png [1.34 KB]](https://www.jdrcables.com/storage/image/core_files/2025/3/11/ea3528007bda13a167a4a722aaf15f8d/png/tfkable/preview/numery17.png)
The mechanical connection point
for a terminated umbilical onto the
host platform or vessel. May include
breakaway system.
![numery18.png [1.45 KB]](https://www.jdrcables.com/storage/image/core_files/2025/3/11/89e5df6b21715d93de681adbe58efc84/png/tfkable/preview/numery18.png)
Connects a Dynamic Bend Strain Reliever to the base of an I or J-tube or FPSO. May include a breakaway system.
![numery19.png [1.48 KB]](https://www.jdrcables.com/storage/image/core_files/2025/3/11/af1ae6f84b6ace2e0564aecb6859ac49/png/tfkable/preview/numery19.png)
Controls bending strain in the umbilical by providing a localised increase in stiffness.
![numery20.png [1.58 KB]](https://www.jdrcables.com/storage/image/core_files/2025/3/11/32792ae8d1683948e6bc363d6bce40f6/png/tfkable/preview/numery20.png)
(UTH) or cobra head
A Remotely Operated Vehicle (ROV)
operated stab plate attached to an
umbilical or HFL.
![numery21.png [1.42 KB]](https://www.jdrcables.com/storage/image/core_files/2025/3/11/643d71960e50f21bb0e268200c34753e/png/tfkable/preview/numery21.png)
An umbilical attachment that
provides positive buoyancy and
minimises movement of a dynamic
umbilical installed between a floating
facility and the seabed.
![numery22.png [1.38 KB]](https://www.jdrcables.com/storage/image/core_files/2025/3/11/6bf2bef5fa638505779046d33d27000d/png/tfkable/preview/numery22.png)
Subsea structure providing stability to an SUT where seabed conditions require the load to be spread across a large area to ensure seabed stability.
![numery23.png [1.59 KB]](https://www.jdrcables.com/storage/image/core_files/2025/3/11/972f0a903637667df5a558477ec7c948/png/tfkable/preview/numery23.png)
(SUT)
Enables multiple wells to be controlled via one umbilical or connects and distributes umbilical functional lines to other subsea equipment, manifolds and trees.
Expert solutions across the full lifecycle
JDR provides a comprehensive solution for oil and gas operators, encompassing the design of cable and umbilical systems, manufacturing, and offshore installation support.
Comprehensive product and offshore services approach
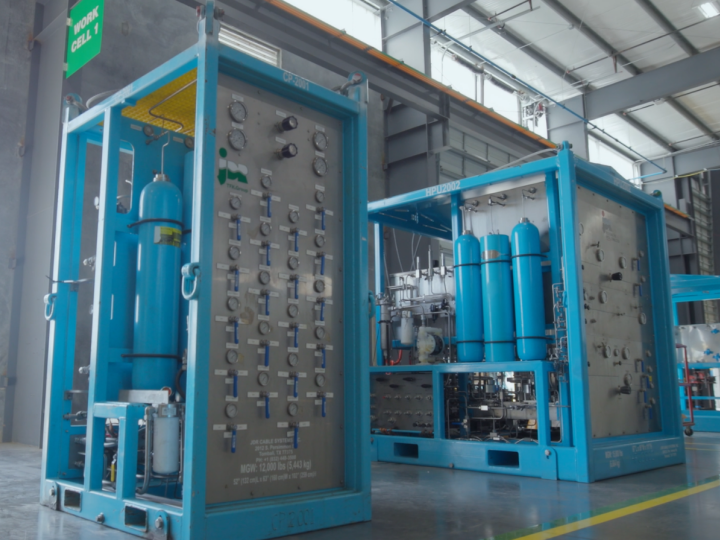
Engineering Expertise
JDR’s in-house engineering team boasts a proven track record in developing and delivering customer projects. Leveraging our expertise in cable design and specialist knowledge of termination components, we collaborate closely with our customers throughout the design phase. We provide comprehensive dynamic analysis, fatigue analysis, and seabed stability analysis to confirm the suitability of our product designs. Full suite of qualification testing is available to validate our design analysis work and manufacturing processes. Our engineers are dedicated to develop innovative solutions that enhance long-term product performance and meet evolving industry needs.
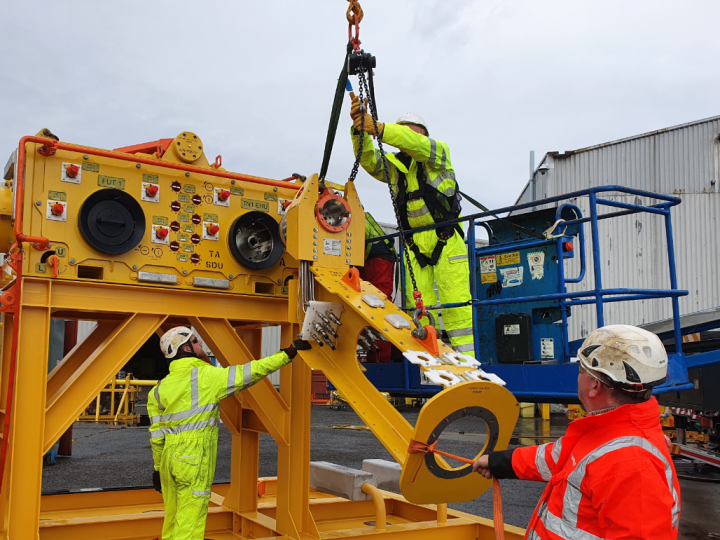
Key achievements and advancements in JDR’s contribution to oil&gas sector
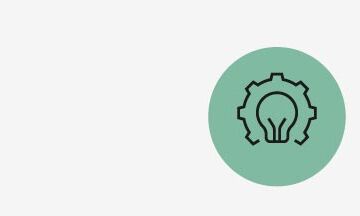
Enabling production of longer length cables without inline factory joints in the components. Thereby reducing cost and machine down-time and increasing production capacity and reliability.
2024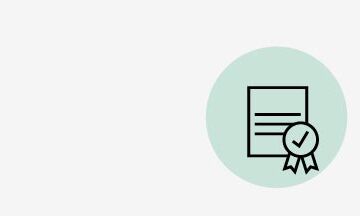
Patent granted for high strength steel tube termination solution, supporting JDR's development of steel tube umbilicals for deeper water depths.
2023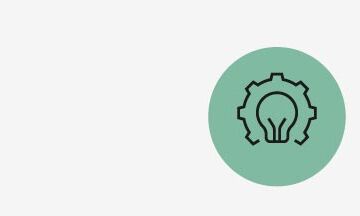
Key milestone with the installation of a state-ofthe-art 16-carrier HLM at Hartlepool facility. This advancement significantly enhanced JDR`s manufacturing capacity, allowing for the production of complex configurations of steel tube umbilicals.
2016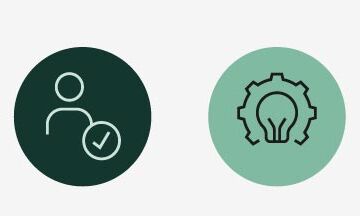
1st Steel Tube Hybrid Umbilical incorporating a combination of steel tubes, thermoplastic hoses, LV cables and fibre optic cables.
2014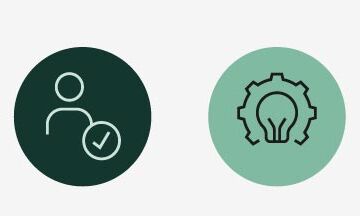
Multiple Deepwater ESP Pump Umbilicals, including full qualification of LV cable inline factory joints.
2011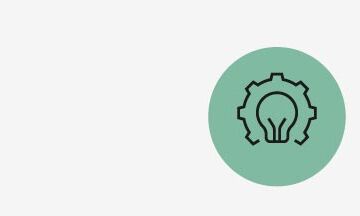
Key test results of an umbilical system include achieving a Tensile Break of 441 kN, a Termination Break of 338 kN, and enduring 500 cycles at 100 kN during Fatigue Testing. Post-test dissection revealed minor fiber dusting, with the strength remaining 95% intact. Prototype qualification was successful in January 2010.
2010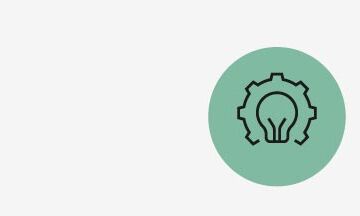
Machine upgrades enabling increased layup production capabilities.
2010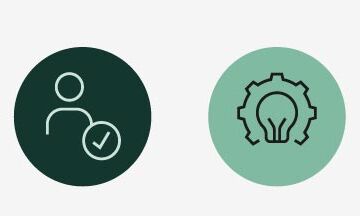
1st Subsea Power Cable manufactured in Hartlepool
2009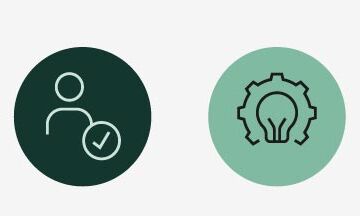
First project utilising JDR’s newly patented IWOCS Self Supporting Umbilical with double donut high strength termination.
2009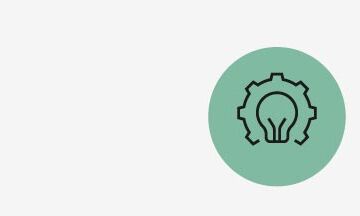
This milestone represents a significant advancement in subsea technology, combining the flexibility of a thermoplastic umbilical with the leak-tight reliability of a steel tube umbilical. It proves substantial enhancements in safety, reliability, and environmental protection for customers’ installations, establishing a new standard in offshore operations.
2007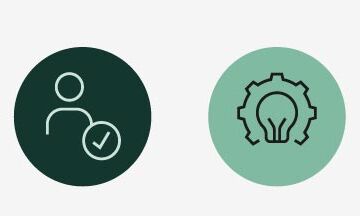
First JDR/WD Close IWOCS Umbilical supplied with integrated Reeler System. This important milestone marks the start of JDR’s capability to supply the completed umbilical & reeler system.
2006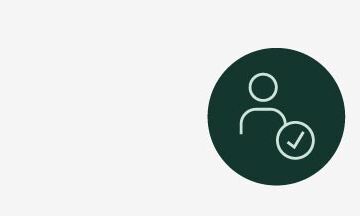
Integrated Test Tree Umbilical and NIM Reeler Systems.
2004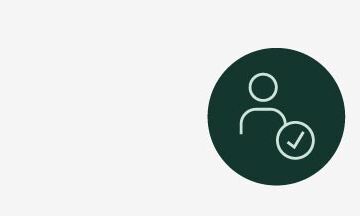
JDR made a significant milestone in 1993 by supplying its first Dynamic subsea control umbilical for BP’s Swift project. This marked a crucial step forward in subsea technology, showcasing advancements in control systems and underwater infrastructure.
1993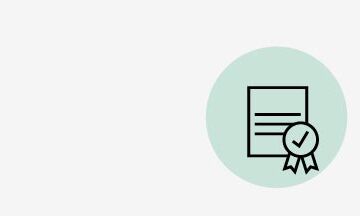
Patent application submitted for an innovative thermoplastic hose liner solution allowing HCR hoses to be vertically deployed at deeper water depths in annulus umbilicals.
2024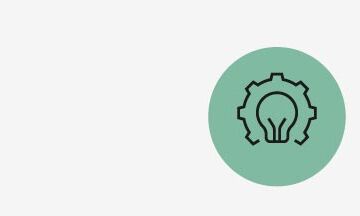
JDR maintain a long term commitment to technical excellence through extensive representative testing using our in-house test rigs at the Littleport Facility.
2016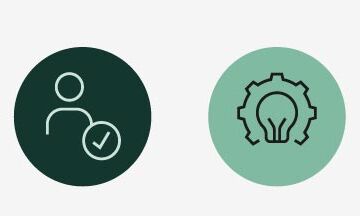
1st Steel Tube Flying Lead project.
2015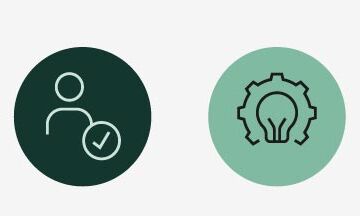
Self Supporting Piling Hammer Umbilical, utilising bespoke terminations which incorporate dual redundant LV cable longitudinal water-blocking at the subsea end.
2013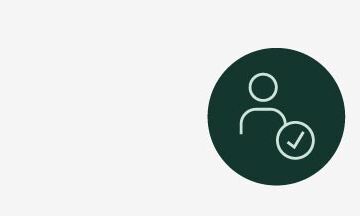
Largest 10 x IWOCs Umbilical and Reeler Project.
2010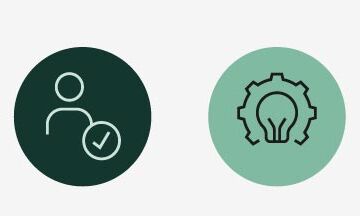
First wave energy project, utilising bespoke designed, application specific, subsea dry-mate connections.
2010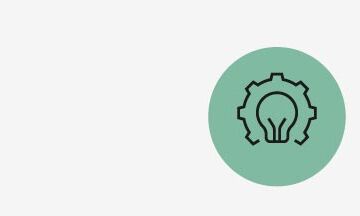
Enabling cost effective production of cables and significant expansion of manufacturing capacity.
2009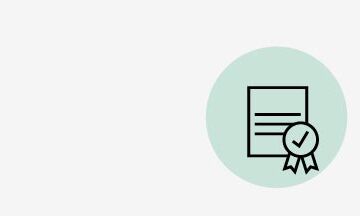
Patent granted for double donut style termination system for open water IWOCS umbilicals more efficient and safer intervention operations and deeper water depths.
2009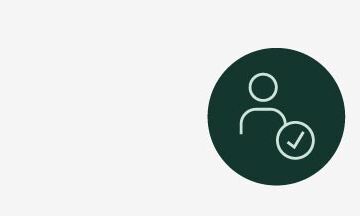
Dynamic Thermoplastic Production Umbilicals.
2008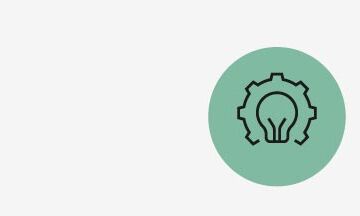
With a diverse range of pre--qualified hoses for offshore use. Our standard, medium, and high-collapse hoses cater to shallow to ultra-deepwater projects in the GOM, Brazil, and West Africa. Currently we can offer hoses up to 20,000 psi working pressure for HT/HP projects, ensuring suitability for 90°C operational temperature.
2007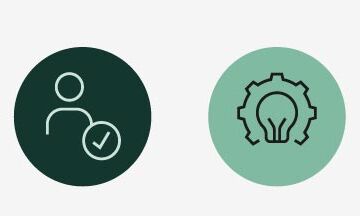
First Dynamic Thermoplastic Production Umbilical.
2004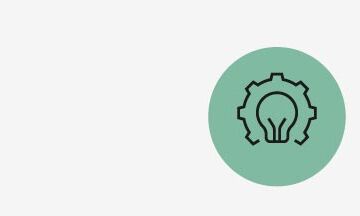
Enabling production of IWOCS umbilicals, SPU and SSIV umbilicals in addition to thermoplastic hose and LV cable components.
2001Enabling production of longer length cables without inline factory joints in the components. Thereby reducing cost and machine down-time and increasing production capacity and reliability.
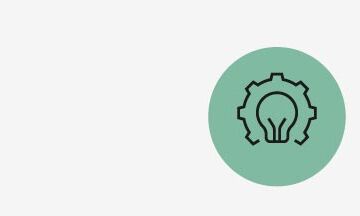
Patent application submitted for an innovative thermoplastic hose liner solution allowing HCR hoses to be vertically deployed at deeper water depths in annulus umbilicals.
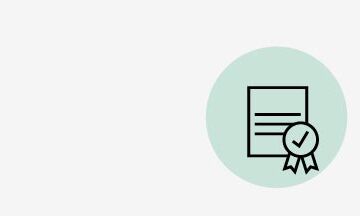
Patent granted for high strength steel tube termination solution, supporting JDR's development of steel tube umbilicals for deeper water depths.
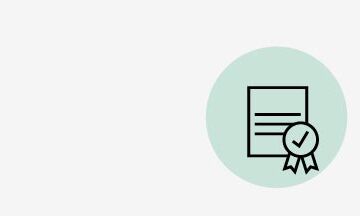
JDR maintain a long term commitment to technical excellence through extensive representative testing using our in-house test rigs at the Littleport Facility.
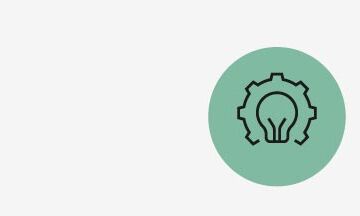
Key milestone with the installation of a state-ofthe-art 16-carrier HLM at Hartlepool facility. This advancement significantly enhanced JDR`s manufacturing capacity, allowing for the production of complex configurations of steel tube umbilicals.
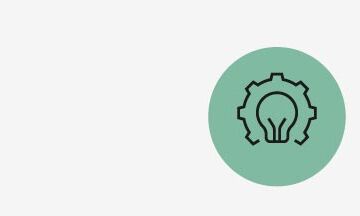
1st Steel Tube Flying Lead project.
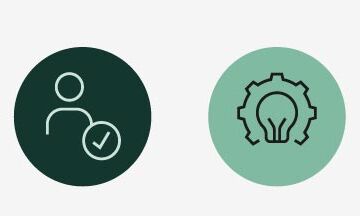
1st Steel Tube Hybrid Umbilical incorporating a combination of steel tubes, thermoplastic hoses, LV cables and fibre optic cables.
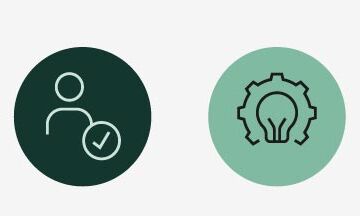
Self Supporting Piling Hammer Umbilical, utilising bespoke terminations which incorporate dual redundant LV cable longitudinal water-blocking at the subsea end.
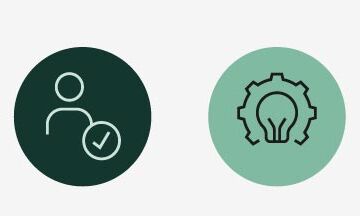
Multiple Deepwater ESP Pump Umbilicals, including full qualification of LV cable inline factory joints.
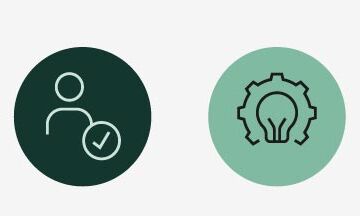
Largest 10 x IWOCs Umbilical and Reeler Project.
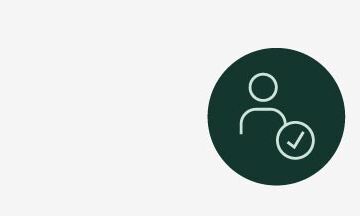
Key test results of an umbilical system include achieving a Tensile Break of 441 kN, a Termination Break of 338 kN, and enduring 500 cycles at 100 kN during Fatigue Testing. Post-test dissection revealed minor fiber dusting, with the strength remaining 95% intact. Prototype qualification was successful in January 2010.
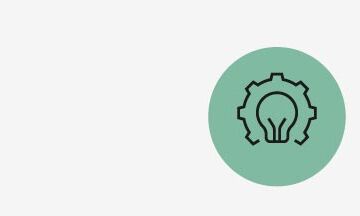
First wave energy project, utilising bespoke designed, application specific, subsea dry-mate connections.
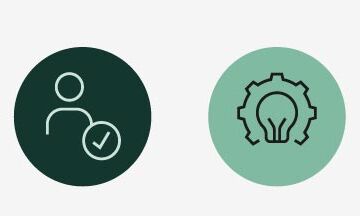
Machine upgrades enabling increased layup production capabilities.
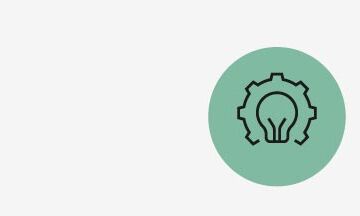
Enabling cost effective production of cables and significant expansion of manufacturing capacity.
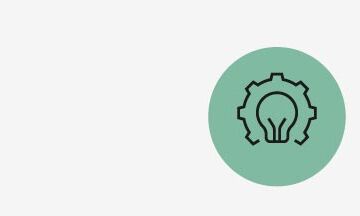
1st Subsea Power Cable manufactured in Hartlepool
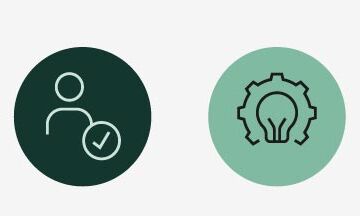
Patent granted for double donut style termination system for open water IWOCS umbilicals more efficient and safer intervention operations and deeper water depths.
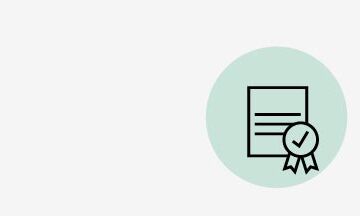
First project utilising JDR’s newly patented IWOCS Self Supporting Umbilical with double donut high strength termination.
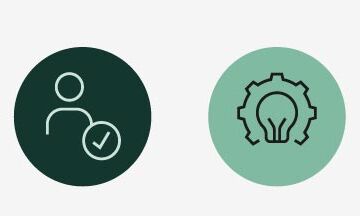
Dynamic Thermoplastic Production Umbilicals.
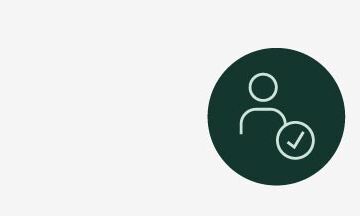
This milestone represents a significant advancement in subsea technology, combining the flexibility of a thermoplastic umbilical with the leak-tight reliability of a steel tube umbilical. It proves substantial enhancements in safety, reliability, and environmental protection for customers’ installations, establishing a new standard in offshore operations.
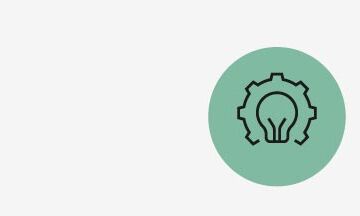
With a diverse range of pre--qualified hoses for offshore use. Our standard, medium, and high-collapse hoses cater to shallow to ultra-deepwater projects in the GOM, Brazil, and West Africa. Currently we can offer hoses up to 20,000 psi working pressure for HT/HP projects, ensuring suitability for 90°C operational temperature.
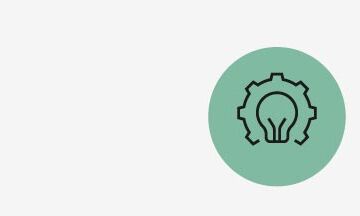
First JDR/WD Close IWOCS Umbilical supplied with integrated Reeler System. This important milestone marks the start of JDR’s capability to supply the completed umbilical & reeler system.
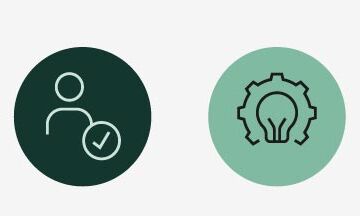
First Dynamic Thermoplastic Production Umbilical.
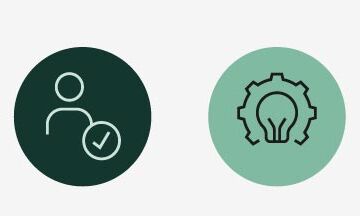
Integrated Test Tree Umbilical and NIM Reeler Systems.
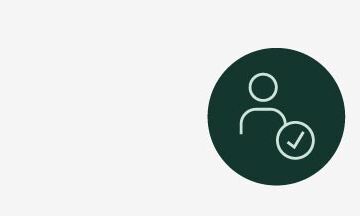
Enabling production of IWOCS umbilicals, SPU and SSIV umbilicals in addition to thermoplastic hose and LV cable components.
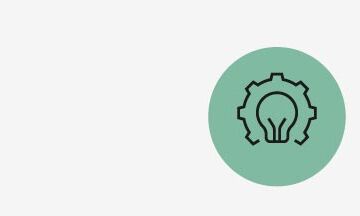
JDR made a significant milestone in 1993 by supplying its first Dynamic subsea control umbilical for BP’s Swift project. This marked a crucial step forward in subsea technology, showcasing advancements in control systems and underwater infrastructure.
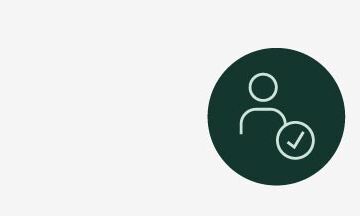
JDR's Cables Typical Constructions
JDR's Cables Typical Constructions
Production umbilical
Thermoplastic hoses: High pressure hoses utilising high strength aramid reinforcement fibres. Customisable for specific project requirements.
Power/signal cables: Excellent communication characteristics with low crosstalk and durable construction. Suitable for highly dynamic environments and for deep waters.
Bundle assembly: Compact construction maximising space utilisation and protecting components.
Strength member package: Contrahelical multilayer construction provides a torque balanced design to provide the required axial strength and umbilical self weight for the specific project environment.
Outer layer: Durable outer jacket to provide wear resistance and to customise umbilical bending stiffness for seabed stability and for dynamic applications.
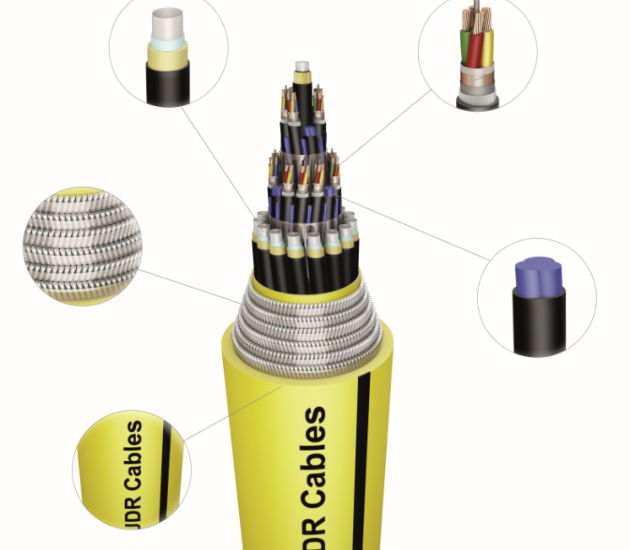
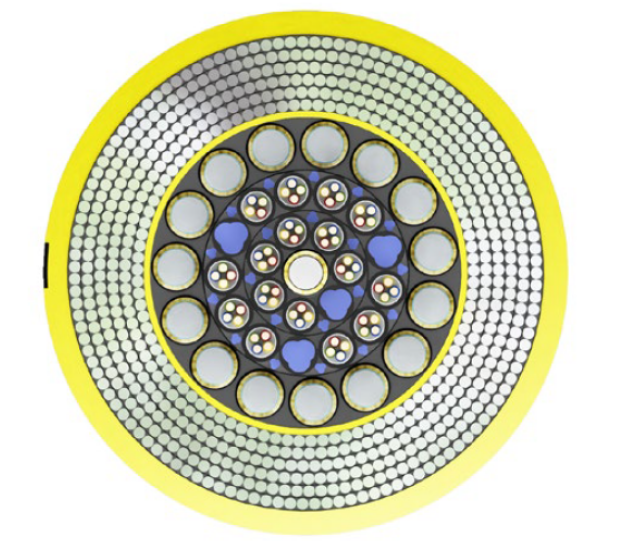
Steel tube umbilical
Steel tubes: Steel tube options for long length applications. Alternative cost effective thermoplastic option where project requirements permit.
Power cores: Utilising high performance superclean insulation system and a market leading semiconductive longitudinal water blocking solution for superior performance.
Bundle assembly: Compact construction maximising space utilisation and protecting components.
Strength member package: Contrahelical multilayer construction provides a torque balanced design to provide the required axial strength and umbilical self weight for the specific project environment.
Outer layer: Durable outer jacket to provide wear resistance and to customise umbilical bending stiffness for seabed stability and for dynamic applications.
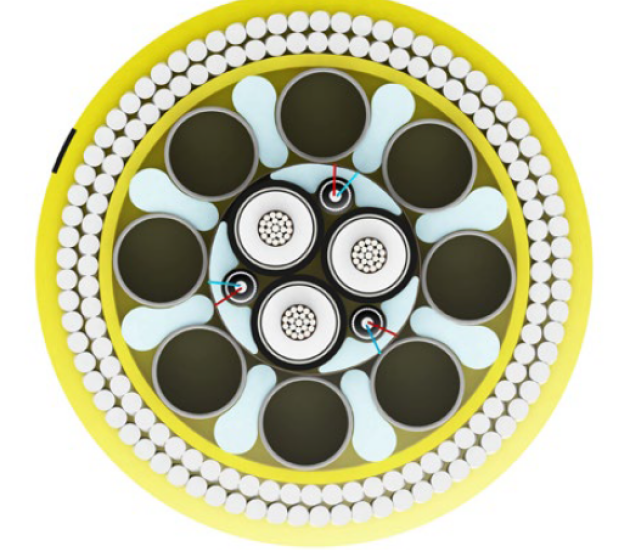
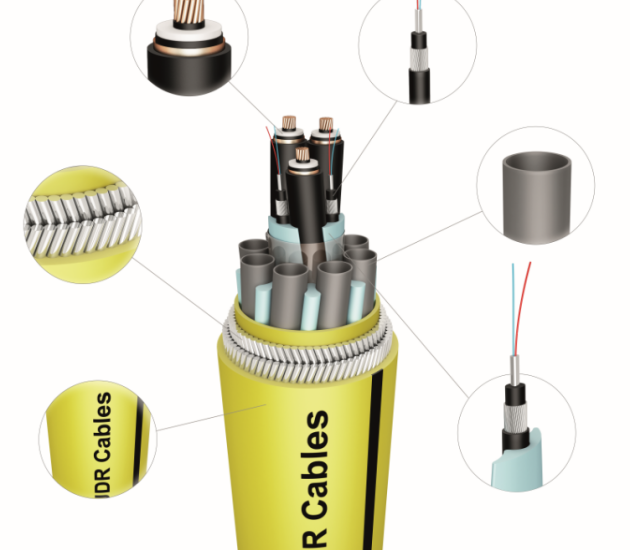
Subsea Umbilicals
JDR is a leading provider of subsea umbilicals, delivering products tailored for a diverse range of offshore oil & gas projects. Engineered to withstand challenging and dynamic subsea environments, our umbilicals ensure critical power, control, and monitoring links, connecting vital components of offshore oil & gas fields.
Our design engineers specialize in creating products that prioritize reliability, minimise project costs, and ensure long-term product lifecycle. Leveraging our expertise in umbilical design, we offer custom-built systems suitable for installation at varying water depths. With a deep understanding of umbilical designs and internal components, we provide customers with the optimal design for the vital connection on your project such as tie-back of subsea trees to fixed platforms, Floating Production Storage and Offloading facilities (FPSOs), and onshore facilities.
JDR-designed subsea distribution units (SDUs) can be seamlessly integrated into project scopes, enabling multiple wells to be controlled via a single umbilical. Additionally, we provide complementary products including steel and thermoplastic Hydraulic Flying Leads and Electrical Flying Leads. This capability is part of a broader range of subsea termination offerings available from the JDR team.
Our umbilical designs incorporate steel tubes and/or thermoplastic hose conduits for hydraulic fluids and process chemicals, and electrical cables for power/signal transmission across gas or oil fields. These advanced components are designed to meet the demands of high-pressure, high-temperature systems, and chemical injection requirements as required.
At JDR, we manufacture our thermoplastic hose and electrical cable components in-house. This provides unequalled product manufacture knowledge and supply control that ensures our subsea umbilical Customers have complete project delivery assurance.
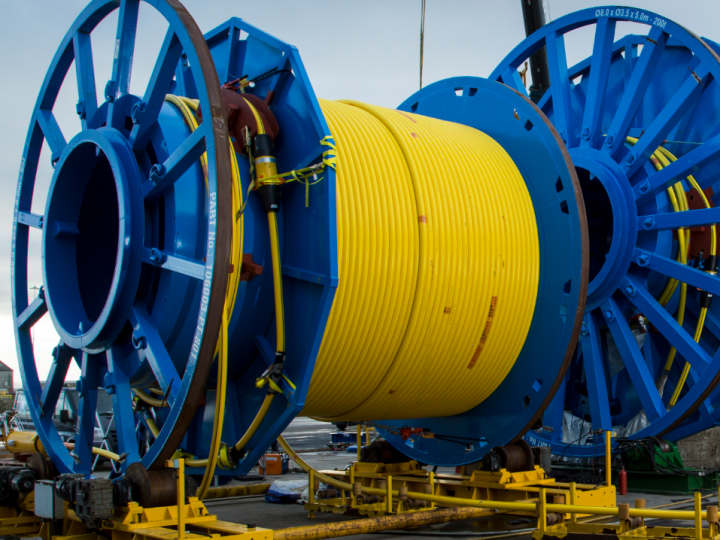
Subsea Power Cables
JDR is a renowned manufacturer of oil and gas subsea power cables, trusted by operators worldwide to distribute power between offshore facilities.
Our subsea power cables are designed to cover great distances and operate reliably in dynamic subsea environments for extended periods. With a strong track record in developing and delivering highly engineered subsea power cables across diverse applications.
Each of our cables designs is meticulously engineered and rated to meet the specific power requirements of our customer’s applications. We provide a range of subsea power cable solutions, which may include fiber optic communications between fixed and floating offshore installations and subsea infrastructures.
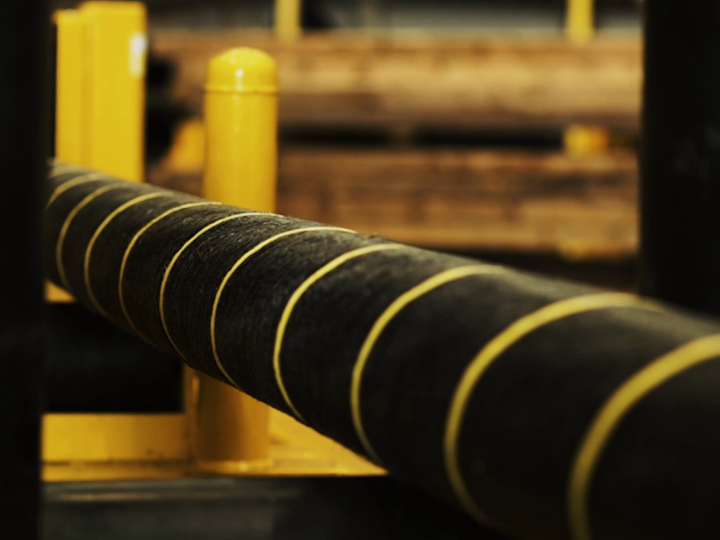
JDR engineering team develops subsea power cables with:
- Flexibility in materials selection and configuration of manufacturing processes, such as a variety of polymer options
- Multi-phase AC systems with a voltage range of 1kV to 72kV
- Both "wet" and "dry" design types using either EPR or XLPE three-layer insulation systems
- A range of armour options to suit static or dynamic applications and varying water depths
- Coilable and non-coilable designs
- Termination design and fitting for topside and subsea connections
- Assembly, qualification, and in-house testing to minimize the risk of commissioning delays.
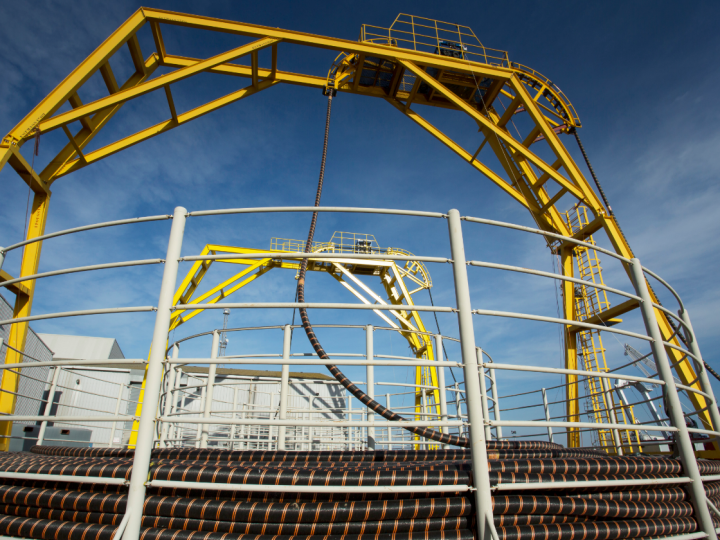